Service and Support
Partner rather than supplier
The ACTIA Group supplied high-tech electronics to the automotive and heavy truck markets since 1986. We have a tradition to work in close collaboration with our customers in order to create an efficient, transparent and agile way of working to create successful projects. ACTIA understands the customers’ needs and is able to provide the right optimized technological solution for every need. We are committed to be a strong and competent partner thanks to our expertise, a complete service offer and automotive quality.
Experts are talking to experts
At ACTIA, we know that every complex project is a bit of an adventure: driving innovation, choosing the right technology, being under tight deadlines and optimizing prices. Project has many interdependencies & interconnections.
At ACTIA, we support you thanks to our capabilities in many fields.
At ACTIA, we support you thanks to our capabilities in many fields.
- Cross-segment presence in passenger cars, trucks, bus & off-highway equipment,
- Expertise in on-board system for the heavy-trucks, bus, off-highway markets segment,
- Cautious approach in the choice of material and certain components (Conflict Mineral Policy),
- Expertise in engineering advanced systems (HW, SW),
- Expertise in Electronic/Electrical Commercial Vehicle Architecture
- Capability to design to ASIL-B and ASIL-C Safety level,
- Expertise in telematics & cybersecurity,
- Expertise in power management
- Expertise in diagnostics (on-board & off-board),
- Expert in plant-cross manufacturing,
- Expertise in obsolescence management for trucks & aeronautics, military, nuclear
A complete service offer: from design to the end of life with long-stang support
More than a high performing supplier, ACTIA is a longstanding partner to OEMs, adding a real business value to the projects.
Your exigence is ours. Our belief is that a collaboration drives growth, profitability and continuous improvements.

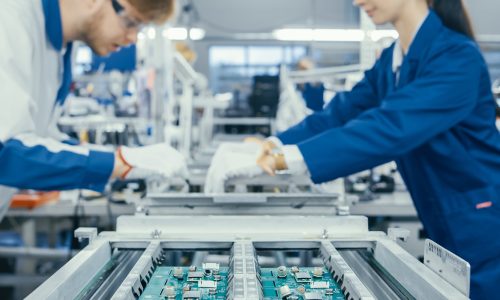
A global footprint
ACTIA has actively been expanding its global footprint around the world and has developed a strong international presence. We now count 24 ACTIA companies in 16 countries which perform electronics development and design. We have representatives in more than 140 countries. This customer-orientated international culture has one goal: support our customers locally and assist them in their global ambitions.
Integrated engineering team for long-standing-support and a better flexibility
ACTIA has a dedicated quotation organization who actively works on a cost-effective common design for variants & options. We propose alternative strategies (technology and architecture choices) to optimize product performance, industrialization & manufacturing. At this step, jointly with customer engineering team, we together work on opportunities for cost reductions. Goal is a maximal customization at better cost, for a smooth Start Of Production. Project teams are accustomed to work with many entities inside the customer’s Group.
Manufacturing in various locations for cost efficiency
Our manufacturing plants are state-of-the-art and approved by a large number of high demanding OEMs. ACTIA’s plants are located in France, the USA and Tunisia to support our customers with local manufacturing. Final assembly facilities are also located in most of ACTIA companies worldwide.
We have a total plant-cross manufacturing capability of over 20 000 sqm2, 12 SMD lines (including single & dual lines). More than 7 million ECUs are manufactured yearly in our plants.
ACTIA industrial strategy focus on modularity in all plants through Plug & Play Easy Dupplicable Single Lane, Single High Mix or Dual Lane (DDL) concept. The same DFM rules applies at all our plants, which facilitates transfer of production between plants.
This high & adjustable production capacity brings flexibility to our global customers who need productions close to their own customers. In our ISO27001 certified plants, we can develop add oc Customer IT management if required, such as Cybersecurity, Encryption, etc.
Supply chain & logistics adapted to demanding oems
ACTIA group’s international presence is an integral part of our company culture. This international dimension serves our supply chain Management. Component reliability analysis, which is essential to the product development methods, enables us to select and design the solutions and components adapted to your needs.
We have EDI capabilities in the whole chain, and ability to pack according to agreement (including management of customer shuttle box).
Our organization, close to the customer, with the goal of delivery quality, reliability & cost-effectiveness has made ACTIA recognized as a leading player within this Automotive sector.
Dynamic operation condition maintenance with long-standing support
Durability experts ensure the maintenance for critical electronic systems: monitoring obsolescence status in advance, processing obsolescence (LBO, long-term electronics component storage, obsolete component replacement, engineering, cloning, redesign). Regular material coverage analysis, including geopolitical impact analysis (ie Brexit) and ACTIA corresponding actions are vital to meet major OEMs’ expectations.
Our environmental policy
We are aware that our activities also have an impact on the environment, and therefore we strive to be recognized as an industrial partner that contributes to sustainable development. The ACTIA Group invests in important environmental protection programs linked to the industrial field.
A hand in hand project with the customer
ACTIA follows a very strict quality plan with the customer, with the goal of 0 production and field issues. ACTIA continuously performs self-assessments. VDA Audits on development, plants and logistics earned us the confidence of Major Automotive Groups since several years. Processes such as Review of Technical Specifications (RTS), Conformity of Production (COP), Part Application Agreement (PAA), Part handling Review (PHR), PPAP for approval of new and modified products and production processes (Customer Product Change request) ensure that the product complies with customer requirements. It is the basis for our customer’s loyalty.
Our team is at your disposal to answer your questions as soon as possible.
Our team is at your disposal to answer your questions as soon as possible.