-
Functional safety
A comprehensive system approach to functional safety expertise
Functional safety is the ability of a system to perform the required functions under specified conditions. It mainly consists of four components: reliability, maintainability, availability and safety.
The integration of various technologies into vehicles, including information technology and electronics managed by computers, means that the systems are increasingly complex. They include a larger number of interacting elements. These systems have intricate behaviours that make them harder to predict. While systems become more and more complex, the competitiveness of the global market places ever stricter constraints on electronics technicians regarding cost and time. This dual constraint is all the more real because it concerns the quality of systems, especially when it involves a risk to human lives or a significant financial risk. The functional safety approach allows products to be placed on the market with controlled risks. Functional safety, which is becoming increasingly important in system design, must be included in system engineering processes. The properties of functional safety are the result of interdependencies that exist in the system and in the system’s interaction with its environment. For this reason, ACTIA handles functional safety analysis using a global approach. As with cybersecurity, ACTIA proposes a comprehensive functional safety approach throughout all phases of the product’s life, from design to the end of the product’s life-cycle.
The integration of various technologies into vehicles, including information technology and electronics managed by computers, means that the systems are increasingly complex. They include a larger number of interacting elements. These systems have intricate behaviours that make them harder to predict. While systems become more and more complex, the competitiveness of the global market places ever stricter constraints on electronics technicians regarding cost and time. This dual constraint is all the more real because it concerns the quality of systems, especially when it involves a risk to human lives or a significant financial risk. The functional safety approach allows products to be placed on the market with controlled risks. Functional safety, which is becoming increasingly important in system design, must be included in system engineering processes. The properties of functional safety are the result of interdependencies that exist in the system and in the system’s interaction with its environment. For this reason, ACTIA handles functional safety analysis using a global approach. As with cybersecurity, ACTIA proposes a comprehensive functional safety approach throughout all phases of the product’s life, from design to the end of the product’s life-cycle.
As part of its functional safety approach, ACTIA :
- reduces the introduction of development faults in the design of the system, hardware and software,
- analyses all hardware failures and uses technical measures to mitigate those that are unacceptable,
- examines manufacturing process failures and implements measures to detect the deviation zone in this process,
- monitors failures of products in service.
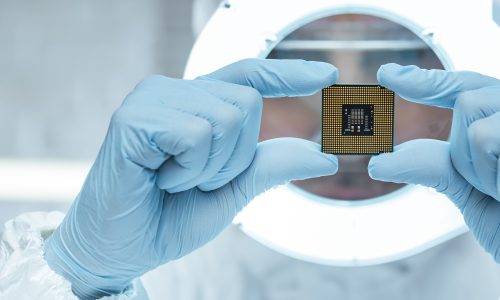
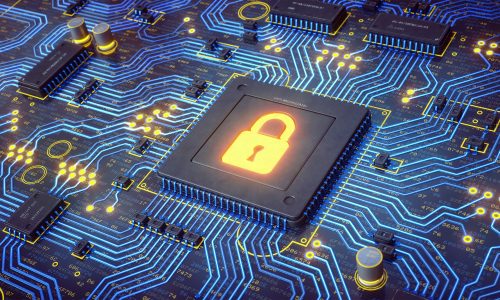
More than a deep know-how, a state-of-mind
With 15 years of experience in safety engineering and manufacturing for agriculture, construction, forklift trucks, handling equipment, equipment for trains and commercial vehicles, ACTIA is no newcomer in the field of functional safety.
ACTIA has developed functional safety for groups of instruments, bodywork and chassis computers, driver train of electric vehicles and safety computers for hydraulic function controls. ACTIA has assisted numerous manufacturers in bringing their machines into line with functional safety standards, in partnership with BUREAU VERITAS, TÜV. ACTIA uses all its know-how and expert resources to manage the functional safety of the products developed. In addition, ACTIA provides support for safety management activities, such as hazard and risk analysis or DFMEA (Design Failure Mode and Effects Analysis): this mode focuses on the design to reduce the risk of product failure.
ACTIA has developed functional safety for groups of instruments, bodywork and chassis computers, driver train of electric vehicles and safety computers for hydraulic function controls. ACTIA has assisted numerous manufacturers in bringing their machines into line with functional safety standards, in partnership with BUREAU VERITAS, TÜV. ACTIA uses all its know-how and expert resources to manage the functional safety of the products developed. In addition, ACTIA provides support for safety management activities, such as hazard and risk analysis or DFMEA (Design Failure Mode and Effects Analysis): this mode focuses on the design to reduce the risk of product failure.
A team dedicated to functional safety
At ACTIA, Functional Safety is a collaborative task that is carried out in a multidisciplinary manner but is supervised by the Project Safety Manager.
The Project Safety Manager is required to direct, supervise, monitor and commission RAMS (Reliability – Availability – Maintainability – Safety) studies for products, together with the development team. He identifies and documents the parts relating to dependability and does so in accordance with the automotive functional safety standard: ISO 26262. The Project Safety Manager guarantees that the architecture and product development comply with the standard. He is involved right from the stage at which the product architecture is defined and sets the guidelines that must be followed and the constraints that must be respected.
The team works in accordance with these guidelines in order to achieve a high level of functional safety.
The role of the functional safety team
- Enhance the company’s processes, methods and tools to improve the overall implementation of functional safety,
- Assist in defining customers’ safety objectives and requirements,
- Interface with the customer throughout the duration of the project.
- Manage the development of products according to the current safety standard,
- Help to define the safety architecture within the products (telematics, I/O controllers, drive train, HMI, etc.),
- Conduct safety analyses, audits and assessments,
- Manage product certification according to the safety standards (ISO 26262, ISO 13849, ISO 25119)
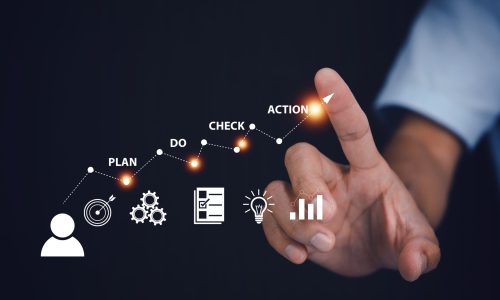
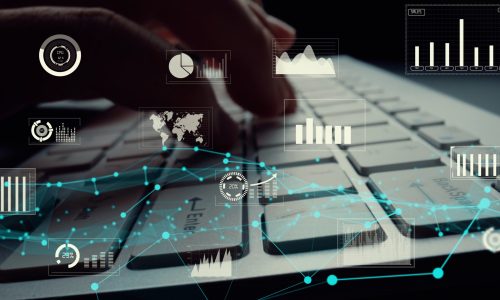
A powerful management tool
Functional Safety standards, including ISO 26262, are complex. To comply with multiple functional safety standards, ACTIA uses suitable procedures and tools. ACTIA has, in particular, developed its own risk analysis tool. It can calculate the metrics required by ISO 26262, among other things.
This tool allows ACTIA to concatenate three analyses in a single tool:
This tool allows ACTIA to concatenate three analyses in a single tool:
- DFMEA,
- FMEDA (Failure Modes, Effects and Diagnostic Analysis): ISO 26262, ISO 13849 and ISO 25119 metrics),
- DFA (Dependant Fault Analysis: Analysis of common failure modes).
- Target the key contributors responsible for “non-safety”,
- Understand the causes of the risk: complexity, lack of testing, lack of diagnostics, poor reliability, etc.
- Implement actions, which can be assurance actions (tests, analysis, etc.) or technical measures (additional diagnostics).